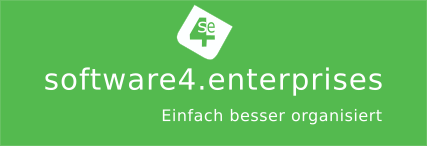
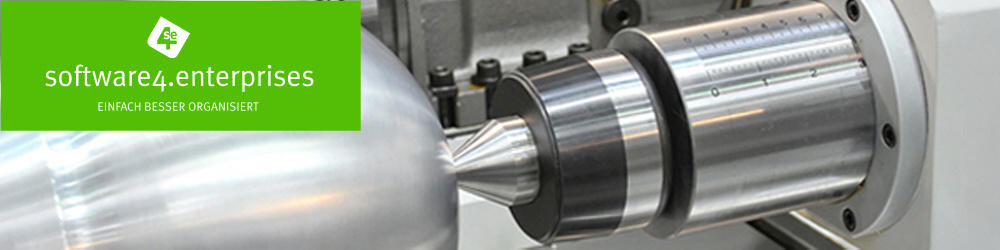
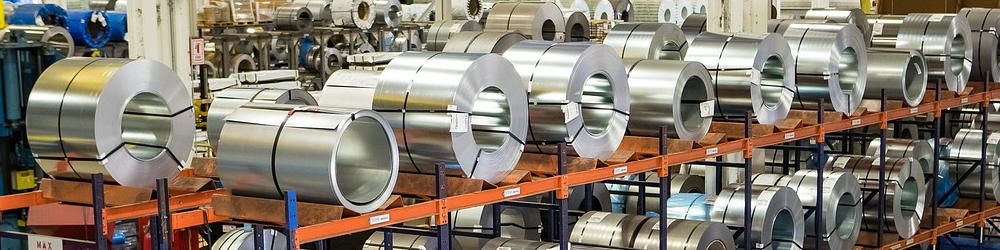
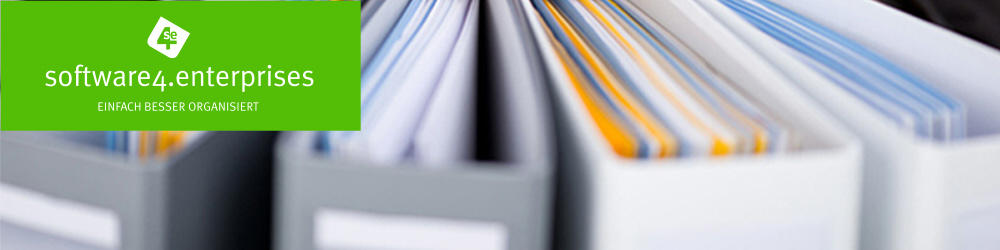
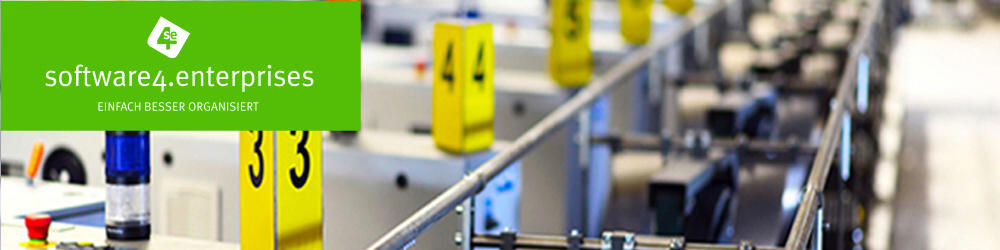
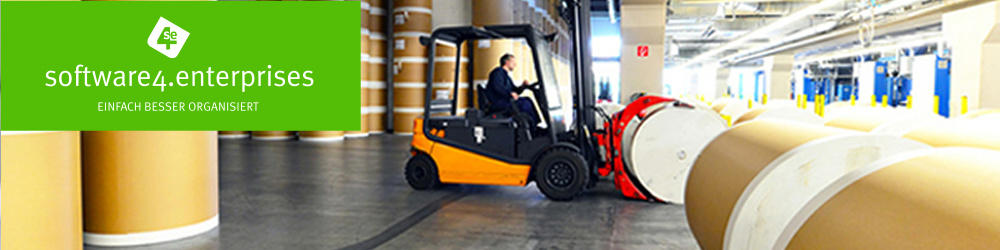
We would like to briefly introduce you to our business areas:
- Software product line kolibri
- Consulting services for kolibri
- Software development to maintain and expand kolibri
- News: The minimal mail application integrated in Web Customer-care supports now the verification of the origin of mails with Dkim
If you have any further questions, please do not hesitate to contact us by phone or email see contact.